When Romain Grosjean’s Haas car split in two and burst into flames during the 2020 Bahrain Grand Prix, it was the titanium halo that ultimately saved his life. But what few people know is that a groundbreaking welding technique played a crucial role in making the halo strong enough to perform as designed in that terrifying moment.
The halo, now an essential part of Formula 1’s safety package, faced strong opposition when it was first introduced in 2018. However, several high-profile crashes – including Grosjean’s fiery accident, Zhou Guanyu’s dramatic flip at Silverstone in 2022, and the Verstappen-Hamilton clash at Monza in 2021 – have since silenced the critics. The cockpit protection device has proven its worth time and again.
But what not many people know is that manufacturing the halo to meet the FIA’s safety standards – to withstand the immense forces it might face, the halo had to be capable of supporting the weight of a London double-decker bus – posed a major technical challenge, one that traditional production methods couldn’t solve. This required not only high-grade titanium but also a flawless, innovative welding process to preserve the material’s properties.
The challenge of welding titanium
By the end of 2017, the companies that participated in the FIA’s tender for the production of the halo – including the party that ultimately won the contract – did not have the in-house technical capabilities to weld the five titanium parts of the halo to the highest possible quality. That’s when they turned to LKN WeldTitan, the titanium-specialized division of Dutch company LKN WeldCompany BV. After nearly four weeks of intensive research and development, they succeeded in welding the parts together in a way that completely preserved the titanium’s technical properties, ensuring that the halo met FIA’s stringent standards.
“Titanium is a reactive metal, which means it reacts with elements in the air – even at room temperature, in a sense that oxidation occurs,” explains Patrick Wouterse, founder and CEO of LKN WeldCompany, speaking to Autosport. “That’s why it’s highly resistant to corrosion: once a thin oxide layer forms, it protects the metal from further oxidation, a property that makes titanium ideal for chemical industries.”
Zhou Guanyu, Alfa Romeo C42 crashes at start of race
Photo by: Mark Sutton / Motorsport Images
But for the halo, the key property wasn’t just corrosion resistance but the strength-to-weight ratio. “Titanium, especially the grade 5 alloy used for the halo, is much stronger than steel while being significantly lighter,” Wouterse continues. “Where you’d need 15 millimetres of stainless steel for a certain strength, you might only need 5 millimetres of titanium. That’s why it’s used extensively in aerospace and why it was chosen for the halo. You want the strongest possible structure without adding too much weight to the car.”
However, welding titanium is a delicate process, as heating the metal causes it to become even more reactive, making it absorb elements like oxygen and hydrogen “like a sponge in a bucket of water”. Even the slightest contamination, such as microscopic traces of dirt or oils from a fingerprint, can already have disastrous consequences for the strength of the titanium in the area where the weld is.
“Once titanium absorbs these elements, it changes the metal’s composition and weakens it dramatically, up to 75% in the affected area,” Wouterse explains. “To prevent that, you need to create an environment where, during welding, no other elements can reach the metal.”
The innovation: a flawless welding process inside a purge chamber
Normally, welders protect the area with a local flow of inert gas, like argon, to shield the molten metal. But with titanium, that’s not enough. “The heat radiates outward — the surrounding material can reach 1,000 degrees Celsius. But at just 150 degrees, titanium already starts absorbing oxygen,” says Wouterse.
“You can actually see the damage — the titanium changes colour. Silver means the properties are intact, while gold indicates that there has been a very slight but acceptable deterioration. But if it turns blue, purple, or green, the material is essentially ruined.”
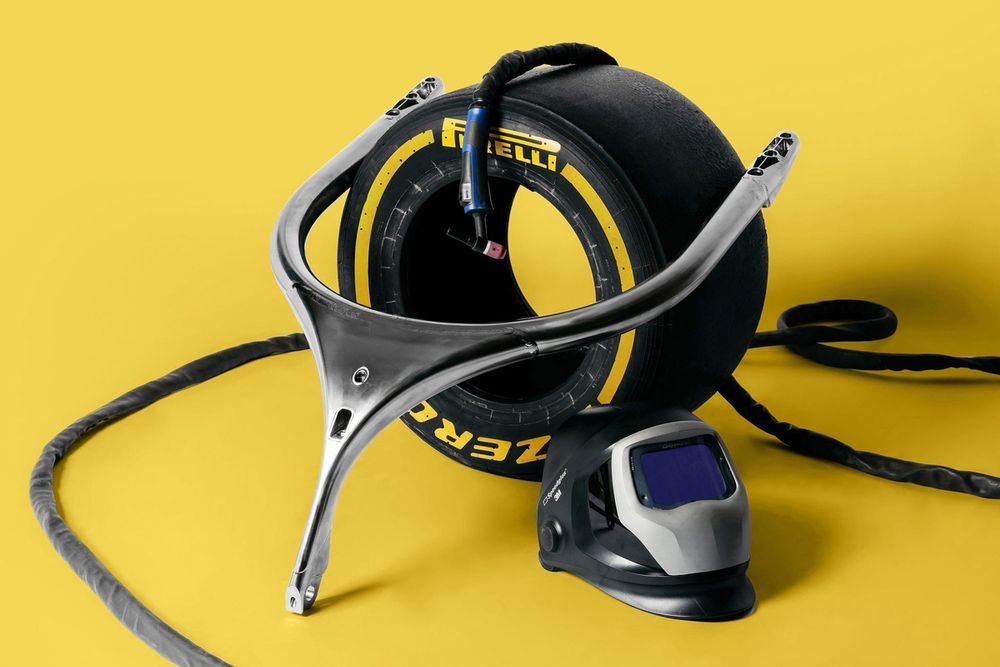
Titanium halo
Photo by: LKN WeldCompany BV
To solve this, Wouterse and his team spent years perfecting a unique welding process, building specialised welding purge chambers, so the welding can take place in an atmosphere of inert gas.
“It sounds simple – just put the parts in a box and fill it with argon – but it’s extremely complex,” Wouterse says. The problem is that there always remains a small amount of oxygen in the purge chamber. “We fill the chamber mainly with argon, helium and neon. But argon is heavy, oxygen is light, and helium is even lighter. Even the slightest turbulence from moving your hands inside the gloves can mix the gases and raise oxygen levels.”
“We had to find ways to get the oxygen concentration down to just a few parts per million,” Wouterse continues. “Everything, from the shape of the chamber to the wall finish, affects the result. So that’s all very complicated. And there are at least fifteen other variables that all have to be perfect to get the right values.”
Over the past two decades, Wouterse has specialised in this process. Through LKN WeldCompany BV, he has built a strong reputation, leading to global demand for his company’s expertise in specialised welding projects across industries such as aerospace, energy, chemical, nuclear, pharmaceutical, and automotive. In addition, Wouterse is frequently hired by companies for process development and quality control.
After FIA’s halo supplier reached out to LKN via a mutual connection, the Amersfoort-based company developed a custom welding chamber large enough to house the entire halo jig, taking into account the structure’s complex, asymmetrical hollow design. “We then qualified the process according to EN ISO standards, welded a prototype and tested it – it easily met the FIA’s standards,” Wouterse recalls. “After that, we moved quickly into production. We ended up welding the first hundred halos for Formula 1 in early 2018.”
Romain Grosjean, Haas F1, emerges from flames after a horrific crash on the opening lap of the Bahrain Grand Prix, Marshals attend the accident
Photo by: Andy Hone / Motorsport Images
A life-saving legacy
For Wouterse, seeing the halo in action – especially during crashes like Grosjean’s – is a source of immense pride. “Of course, you always hope nothing bad happens. But when it does, it’s good to know there’s a halo on that car. It makes you proud to think, ‘We helped make that’.
“Especially in the beginning, so many people hated the halo — they thought it was ugly while some of the drivers said it obstructed their view. But after the first big crash where the halo made the difference, all the criticism stopped. Everyone agreed it was the right thing.”
Grosjean’s crash left a lasting impression on Wouterse. “When you look at simulations that were made after the incident, you see how the halo deformed the barrier just enough to protect Grosjean’s head. Without it, he wouldn’t have survived. And because the halo held, he was also able to climb out of the burning wreckage.”
Wouterse even exchanged messages with Grosjean afterward. “I reached out on LinkedIn and explained our role in the halo. He replied, ‘Then I guess I need to thank you.’ As a huge Formula 1 fan myself, that meant a lot.”
Later this year, Wouterse plans to visit the F1 Exhibition in Amsterdam to see Grosjean’s burned-out chassis in person — a powerful reminder of the life-saving technology he and his team helped perfect.
In this article
Be the first to know and subscribe for real-time news email updates on these topics
Subscribe to news alerts
Read the full article here